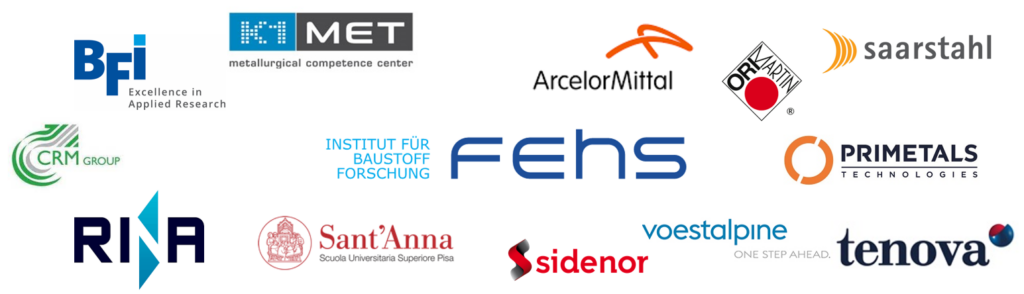
The project brings together 13 partners from Austria, Belgium, France, Germany, Italy and Spain, including 5 steelworks, 6 research and technology organizations (RTOs), and 2 suppliers. In addition there are 3 sub-contractors taking part in the project.
FEhS-Institut für Baustoff-Forschung e.V. (FEhS) is the coordinator of InSGeP project. FEhS is a collaborative non-profit research organization supported by the German, Netherlands, Swiss, and Austrian steel industries. With over 60 years of experience, FEhS is dedicated to promoting and advancing the utilization of slags and residues from iron and steel production. Our institute serves as a central hub for research, development, and the exploration of new applications for these products. FEhS operates in close collaboration with steel companies and other national and European organizations within the steel industry. This partnership ensures that our research activities are aligned with the needs and priorities of the steel sector, facilitating the development of innovative solutions and technologies. Our state-of-the-art laboratories are equipped with advanced analytical techniques and specialized facilities, including melting and heat-treating furnaces tailored to meet various requirements. This infrastructure allows us to conduct comprehensive investigations and analyses, enabling us to explore the potential uses and properties of slags and steel residues. FEhS-Institute is certified in accordance with the Technical Compliance of ISO 17025. This certification underscores our commitment to excellence and precision in our research and testing procedures.FEhS-Institute coordinates the InSGeP project.
Scuola Superiore Sant’Anna (SSSA) is an autonomous, special statute public university operating in the field of applied sciences with the aims of promoting the development of culture, scientific and technological research, and innovation. SSSA will participate to the project mainly through the centre of ICT for Complex Industrial Systems and Processes (ICT-COISP) of the Telecommunications, Computer Engineering, and Photonics Institute (TeCIP). Since its origin, this team focuses its activity in the steel sector, by particularly focusing on the application of advanced modelling and simulations system for monitoring, management, optimization and control of processes for steel production also targeting improved environmental sustainability of the steel production cycle and implementation of Circular Economy and Industrial Symbiosis solutions. Since 2000 the ICT-COISP team participated to 68 RFCS projects (11 ongoing), by coordinating 10 of them, among which iSlag and REUSteel. Within InSGeP two further Institutes of SSSA will provide contribution. The Management Institute contributes to the WP5 (mostly Task 5.3) through its Sustainability Management Laboratory (SUM Lab), which holds a consolidated experience in Life Cycle Analysis and assessment of environmental impact of industrial production cycles and in involved in some ongoing EU-funded projects related to the steel sector. The Crop Science Research Center develops scientific activities covering several aspects of the plant-based food production and supply chain and in the past investigated the use of scrap as fertilising and liming agent on alkaline soils typical of the Mediterranean areas within the RFCS projects SLAGFERTILISER and PSP-BOF. Therefore, it contributes to WP5 (mostly Task 5.1) by developing column tests to preliminarily assess the feasibility of the slag use in agriculture.
RINA-CSM (RINA-CSM) is a research company founded in 1963 by aly’s major steel manufacturers and end-users for the development and application of innovative processes and materials and now part of Rina Group, a global provider of classification, certification, testing, inspection and training services for major industries. CSM research activities are mainly related to modelling and design of materials and products, optimization and development of processes, innovative pilot plants and reduction of environmental impact. With a staff of about 230 researchers and technicians, 20 laboratories, pilot lines and full-scale testing facilities, it is the main reference for projects in which materials, technology and innovation play a critical role. The traditional presence of CSM as the Italian reference pole in European research (RFCS and Framework Programmes) results in hundreds of international collaboration agreements and contracts. CSM is a participant also in the European Technological Platforms like ESTEP (steel) and EuMat (advanced materials) and co-founder of RIES (Research Initiative European Steel). Currently CSM has more than 80 active Grant Agreements with the European Commission.
K1-MET GmbH (K1-MET) is one of the leading European research and technology organisations focusing on metallurgical and environmental process development. With approximately 80 employees at its two main locations in Austria (Linz, Leoben), K1-MET’s research is focused on raw materials and recycling, metallurgical processes (primary metallurgy and secondary metallurgy until casting), low carbon energy systems, as well as CFD and process simulation and data analyses. The pilot plant of a future CO2-free ironmaking using hydrogen plasma (Hydrogen Plasma Smelting Reduction, HPSR) is operated by K1-MET together with voestalpine Stahl and another scientific partner (Montanuniversitaet Leoben, not partner of InSGeP). Within the InSGeP project, K1-MET will produce a HPSR slag for further analyses and will collect data about future iron and steelmaking processes and dedicated expected slag quantities together with voestalpine Stahl. Furthermore, K1-MET will support the search for applications of slag products from next generation ironmaking processes. Apart from that, K1-MET will lead the DEC activities within InSGeP.
voestalpine Stahl GmbH (voestalpine) is a business unit in the Steel Division of the voestalpine Group operating a fully integrated steel mill with an annual capacity of 5.9 Mt steel for flat products. Core aggregates include three blast furnaces (BF) and three basic-oxygen furnaces (BOF) to manufacture and process high-quality hot-rolled and cold-rolled, electrogalvanised, hot-dip galvanised and organic-coated steel strip. voestalpine ranks among the leading suppliers of the European automotive, domestic appliance, machinery, and construction industries, as well as of the energy and gas processing industry. The company’s vision aims at continuous improvement of the steel production process with respect to efficiency, raw materials, sustainability, environment, and climate protection. Perfectly fitting to the ongoing developments of new, breakthrough CO2-saving hot-metal production technologies, such as HPSR, or the Smelter Process to operate low-grade resources, the focus of voestalpine within the InSGeP project is to find application fields of slags generated during these future ironmaking processes.
Centre for Research in Metallurgy (CRM), is a non-profit steel research organisation with a long standing experience in steel research and proven expertise in steel processing and alloy development for major industrial steel groups, among others by a lot of previous ECSC and RFCS projects. CRM has a staff of about 260 persons, half of them being scientist or engineer with large field of knowledge and experience in the steelmaking process, modelling, sensor development or metal application. The group combines skilled and experienced research teams with unparalleled testing facilities covering the whole manufacture chain of metals, from raw materials to advanced steel applications, ranging in size from laboratory scale to pilot and even semi-industrial production lines. Beyond the technical and scientific expertise, CRM was and is still largely involved in ESCS and RFCS projects dealing with EAF process, modelling and control. Also CRM is represented in TGA1 group with an expert in the field of EAF steelmaking. Two of the main European steelmakers (ArcelorMittal and Tata Steel) are the effective members and the closest partners of CRM. In total, more than 40 companies (steelmakers, plant manufacturers, suppliers) are members of CRM. The department “Metal Production and Recycling” involved in the proposal has long time experience in modelling and control of the EAF process. In the frame of InSGeP project, CRM will produce large quantity of DRI-EAF and SAF slags, study the expected future slag rheology and fitting with foaming needs, perform large scale granulation trials and evaluate the possibility to combine these future slags with other by-products to produce higher value materials
Tenova SpA (TENOVA) is a worldwide supplier of advanced technologies, products and services for metal and mining industries. R&D activities are focused on the areas that mostly impact the future of served industries: quality of products delivered by customers, energy saving, environmental safeguard through pollution reduction and residue valorisation. Tenova recently developed a dry slag granulation technology, tested on both LF and EAF slag. Tenova is leader in the design and supply of equipment for the production of crude steel using EAF. Success can be largely attributed to its innovative technology, flexibility to customer requirements and the timely execution of the projects. Tenova innovative DR technology represents the state-of-the-art in DR plants design, operation, environmental friendliness and economy. The ENERGIRON ZR process with no external gas reformer provides unmatched flexibility for any reducing gas source in any region and using the widest range of iron ore feedstock and qualities. The company participated to several RFCS, H2020 and ERDF funded projects also in a coordinating role.
ORI Martin (ORI) was founded in 1933, it developed into an electric furnace steel mill to produce continuous casting billets and hot rolled wire rod, bars in coils and alloy steel bars for special applications in the automotive sector, such as: nuts and bolts, suspension springs, torsion bars, steering components and mechanics in general. It is also fitted with installations for annealing and tempering thermal treatments. The ORI Martin Group’s constant commitment to environmental protection, health and safety at work, is an integral part of the technological development of the whole Group.
VDEh-Betriebsforschungsinstitut GmbH (BFI) is a non-profit institute in Germany, is focused on applied research for the steel industry. The staff of around 100 people is organised in 7 scientific departments and drives in close and interdisciplinary cooperation. 70 % of the staff are scientists and engineers who guarantee, together with technicians and administrative staff, a high level of research quality and project performance e.g., by applying a strict quality management of research proposals and a consequent results-oriented management of projects. Within the InSGeP project, BFI will focus on lab trials in order to provide, analyse and assess slag samples from self-produced DRI, which shall be representative for the future H2-DR route. Further, BFI will assist Saarstahl in evaluation of operational EAF trials for creation and modification of slag samples based on partial HBI input.
ArcelorMittal Maizieres Research S. A. (AMMR) is an international research centre, located in Maizières-lès-Metz, France, belonging to ArcelorMittal group, world leading steel manufacture and representing ArcelorMittal as a single contact point. With about 500 full time researchers, AMMR is one of the biggest R&D centres in Europe. The by-products team involved in the project exists since 2006 and has experience in characterisation, treatment, modification and usage of all kinds of iron and steel by-products. This team is in close relationship with plants and other R&D units of the group, and it will benefit from the support of the corporate By-Products Sales team. This team has also coordinated former European projects, such as ActiSlag. The aim of AMMR within the InSGeP project is to work together with European researchers on the characterisation and possible valorisation of the future steelmaking slags. AMMR will actively participate in sample collection and characterisation and also in slag modification trials (cooling or chemical modifications.)
Sidenor (SIDENOR) is a steel company, leader in the European steel industry for the production of special steel long products. A full range of rolled products (wire rods, bars, flats, billets) as well as cold finished (cold-drawn, peeling/turning and straightening) and continuous casting semi-finished products (billets, blooms and rounds) in carbon steels, free cutting steels, alloyed steels, spring steels, microalloyed steels, cold forming steels… are included in Sidenor´s portfolio. Sidenor´s annual capacity for sustainable steel production is based in an electric arc furnace. It exceeds one million tons, primarily destined to the automobile, machinery, capital equipment, railway, energy, mining and petrochemical industries. By participating in projects such as TRACEX, CORALIS or RE4INDUSTRY, Sidenor works with the entire value chain in order to design and develop increasingly sustainable and environmentally friendly technologies, processes and products. Sidenor´s aim in InSGeP project is to collaborate with European Research Community in characterizing future steelmaking, from the perspective of the Circular Economy.
The Saarstahl Group (SAARSTAHL) based in Völklingen, is specialised in the production of wire rod, bar steel, semi-finished products and high-quality forged products. Saarstahl responds to the global challenges in the areas of mobility, energy efficiency and safety with innovative products and intelligent technologies. Saarstahl products are in demand in the automotive and construction industries, in the power generation sector and in the aerospace industry as well as in mechanical engineering and other steel processing sectors. Saarstahl AG is a subsidiary of SHS Group, which is wholly owned by the Montan-Stiftung-Saar, a private industrial foundation under private law, whose aim is to strengthen and secure the two large steel companies (Dillinger and Saarstahl) on the Saar. SHS Group employs a total of 13,000 people, of which about 900 are in France and 800 are French cross-border workers. Together, the two companies continuously invest in training and further education as well as in the modernisation of their plants and processes. And they are pursuing an industrial digitalisation strategy Industry 4.0. In the last ten years, Saarstahl and Dillinger together have invested an average of about 150 million euros annually. Together with Dillinger Saarstahl will invest in new DRI-facilities and EAF furnaces to produce steel with lowest possible CO2-emissions to achieve the necessary aims to support the reduction of global warming. Our researchers have clearly understood the importance of slags to improve the future steelmaking. These new slags can play a very important role as a raw material to decrease the consummation of natural resources.
Primetals Technologies Limited (PRIMETALS) headquartered in London, United Kingdom, is a pioneer and world leader in the fields of engineering, plant building, and the provision of lifecycle services for the metals industry. The company offers a complete technology, product, and services portfolio that includes integrated electrics and automation, digitalization, and environmental solutions. This covers every step of the iron and steel production chain—from the raw materials to the finished product—and includes the latest rolling solutions for the nonferrous metals sector. Primetals Technologies is a joint venture of Mitsubishi Heavy Industries and partners, with around 7,000 employees worldwide. In this project mainly two locations of Primetals Technologies will be involved: the competence centre for electric steelmaking in Germany and the competence centre for integrated steelmaking and environmental solutions in Austria. Primetals Technologies will be involved in gathering and analysis slag samples for the DRI EAFs installed which use a high share of DRI in the charge mix. It will also make test of future low grade DRI Smelters and will provide slag samples thereof and will provide possible concept for dry slag granulation of such smelter slag.